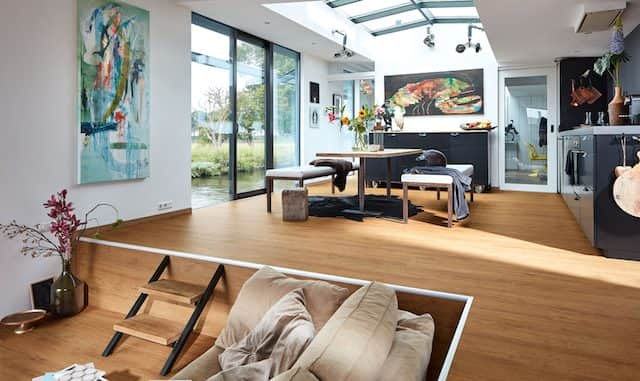
Modular multilayer flooring is becoming more popular by the day because of its product advantages: custom design, easy installation, low installation height and good durability are just some of the benefits of this innovative class of flooring. In previous years, designers have increasingly been focusing on the issues of environmental performance and health in the home. In the MMF sector, both commercial and private users welcome the fact that ecological concepts and materials are continuing to advance.
An increasing number of multilayer floor producers are turning to ecological production processes and biobased product formulations. They use key phrases like “no plasticisers dangerous to health, free of heavy metals, solvents and other harmful substances, whether soluble or volatile”, to highlight the safety of their quality products – invariably certified by recognised ecolabels such as the Blue Angel or the ECO seal, or even international labels like Greenguard in the US or the French VOC label.
Exactly where in product development the fundamental approaches for alternative product formulations and components lie can be clearly illustrated using the example of LVT production. The starting material for conventional LVT production is PVC (polyvinyl chloride), which is obtained from crude oil or natural gas and sodium chloride. Depending on the manufacturing process, fillers and a number of special auxiliary agents and additives are combined with the polymer matrix to match the requirements of the application in terms of processability and technical properties.
Not all plasticisers are the same
As PVC is an inherently hard material, plasticisers are added to make it flexible and resilient, whilst maintaining its shape. Use of the dangerous phthalates EHP, DOP, DBP, BBP and DIBP, which can be toxic to reproductive health, has been restricted in the EU since 2015 and is subject to an authorisation requirement. According to the REACH Regulation (Registration, Evaluation, Authorisation and Restriction of Chemicals), these low molecular weight plasticisers are classified as Substances of Very High Concern (SVHC). Long before the restriction was introduced, a number of manufacturers had already stopped using substances like these. Various alternatives to these plasticisers are now being used in flooring production. One of these is the high molecular weight, more stable C9 and C10 phthalates DINP, DIDP and DPHP, which are recyclable and do not accumulate in either human or animal organisms, although phthalate-free plasticisers such as DOTP and DINCH are also used.
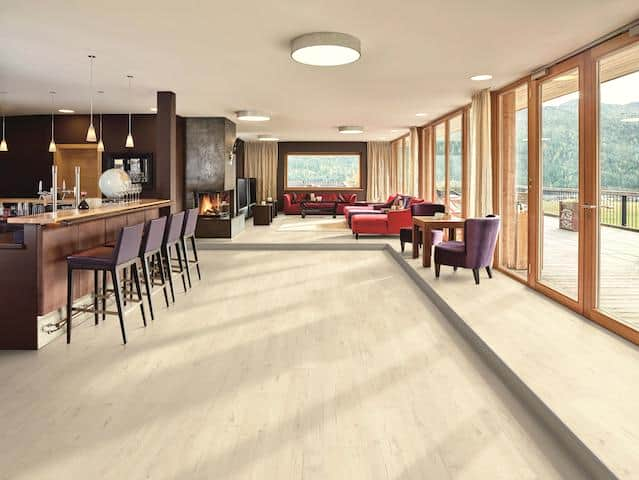
New concepts using biobased plastics
Recently, increasing use has been made of bioplastics/biogenic plastics made from raw materials derived partly or wholly from renewable agricultural or forestry production. Amongst these biogenic materials used for MMF production are plant oil-based epoxies or biopolymers belonging to the group of polyolefins (PO). Biobased PO polymers such as biopolyethylene (PE) and biopolypropylene (PP) are most commonly used as matrix materials. They require no stabilisers and are suitable for mechanical recycling. An EVA copolymer (ethylene-vinyl acetate) works as a binding substance, and natural mineral fillers such as chalk and kaolin are also used.
In the multilayer sector, different concepts have been successfully established for biobased products. The natural polymer lignin can be used as a blend partner for high-quality bio PVC. Further product variants can be manufactured by combining biovinyls with natural fibres (flax and hemp) or cork, for example. Some multilayer floor manufacturers use cork-vinyl mixtures such as these for core materials in their biobased products.
Mineral carrier materials combine many advantages
Natural materials similar to ceramic can also form the basis of semi-rigid MMF substrates. They are light, yet incredibly stable and also waterproof. The individual components are produced at low temperatures, which saves resources and energy and is low-emission. The ecological balance sheet of MMF floors with an HDF core (high-density fibreboards) can also be improved by using wood fibres from sustainably-managed forests and recyclable materials from the timber industry. The use of biodegradable raw materials means that at the end its useful life, this kind of flooring can simply be disposed of as household waste or recycled.
Resource-saving production – non-toxic in use
Enormous progress has been made over the past few years in the area of ecological flooring products, and for modular multilayer floors there is still plenty of potential for development. For all responsible manufacturers, the focus is on making high-performing MMF products that are both environmentally-friendly and safe. In addition to ecologically clean production, a comprehensive understanding of ‘sustainability’ means practising corporate social responsibility, e.g. working with regional suppliers, paying staff an appropriate remuneration, complying with occupational health requirements, avoiding child labour overseas, etc.
As is the case everywhere, environmental protection and ecology begins on the basis of a long service life for products and resource-saving production. In this respect, the members of the MMFA consider themselves to be in an ideal position.